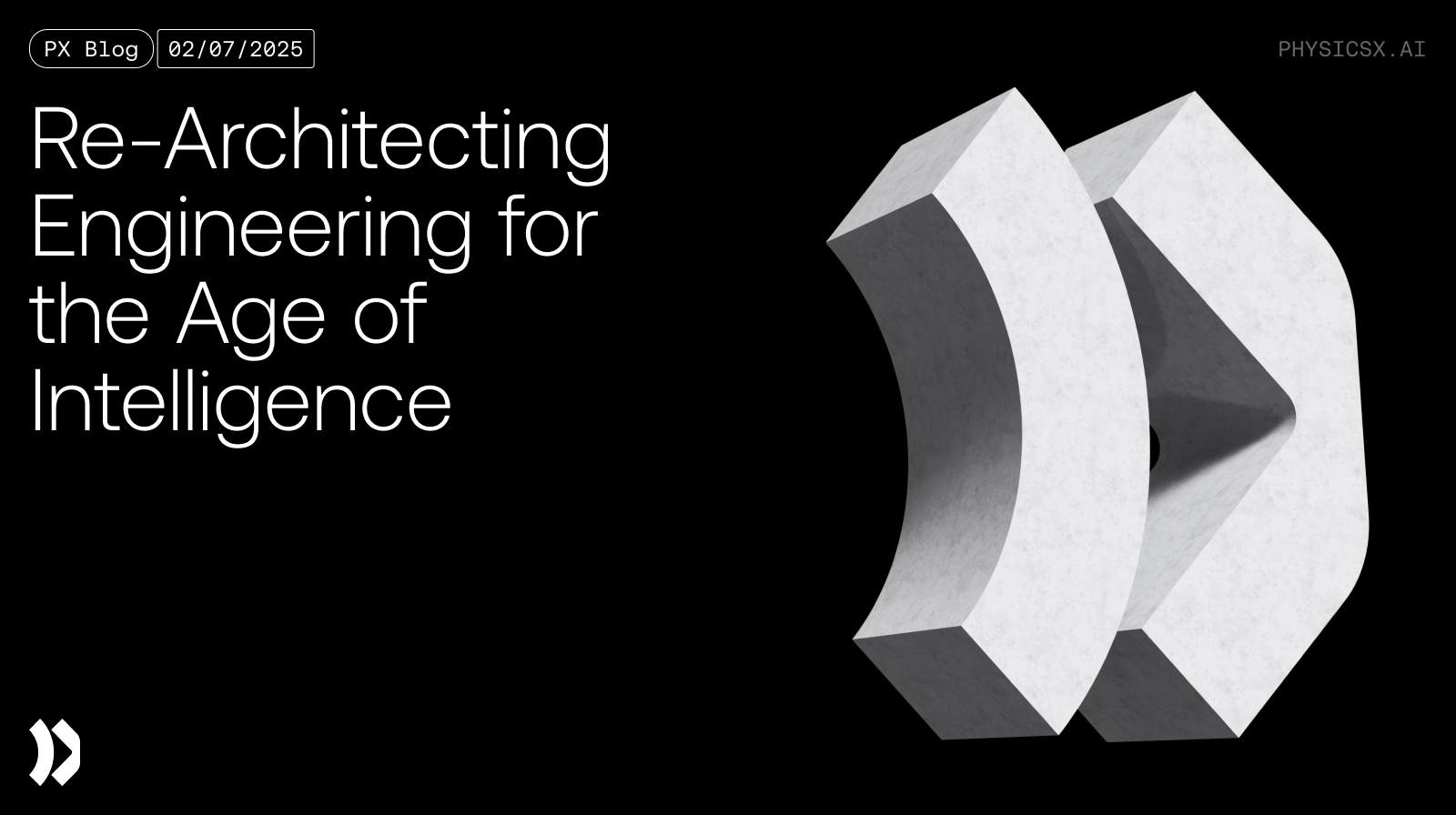
From bottlenecks to breakthroughs: Engineering’s next chapter starts here
Aerospace & defense, automotive, semiconductors, materials production, energy & renewables. These industries are the backbone of our economies and are on the frontline of today’s most urgent challenges — including the climate transition, defense modernization, energy independence, and industrial resilience. At the same time, the companies driving progress in these sectors are underserved by the software on which they rely. Rather than meeting growing complexity and performance requirements, engineering and manufacturing tools exacerbate that complexity. They struggle to meet the speed and fidelity requirements for virtual simulation, complicate processes with multiple handoffs and fragmented workflows, and increase the reliance on specialist roles.
We’ve seen AI transform how we write, code, analyze data, and change the nature of how we collaborate in many domains. But many of the most important problems don’t live in text editors — they’re found in wind tunnels, clean rooms, factories, and labs.
This is the gap PhysicsX is closing. We’re building the software stack to bring AI-native capabilities to the entire engineering lifecycle, enabling AI-driven simulation acceleration, automation, optimization, and control across the most critical problems advanced manufacturers face.
The motivation for an AI-native engineering software stack
Insofar as engineering involves designing, making, and operating machines and structures, it centers on performance evaluation. And many of the core aspects of performance are grounded in physics and chemistry, like heat transfer or mixing between two liquids or a structure’s ability to withstand loads. Today, these are typically evaluated through a combination of numerical simulation and physical testing. In high complexity settings, both represent fundamental bottlenecks. Physical testing is constrained by the need for hardware: building physical prototypes, test rigs, and wet labs. Numerical simulation, on the other hand, is incredibly compute-intensive and time-consuming.
We’re setting out to transform engineering by rethinking how physics simulation is done in engineering and manufacturing workflows, shifting it from numerical simulation and physical testing to inference with AI. Doing that unlocks three things:
- Expanded frontiers for end-to-end automation and optimization: Compared to numerical simulation, physics by inference enables a dramatic acceleration — between 10^4 and 10^6 across different physics — vastly improving our ability to search high-dimensional spaces, including generatively, and to do end-to-end optimization simultaneously for multiple performance criteria and constraints.
- Improvement rates coupled to data and compute: Numerical simulation is invariably coupled to our best understanding of the equations of physics governing some phenomenon. As such, improvements are slow and rate-limited by fundamental scientific discovery. Physics simulation by inference involves AI models trained on a corpus of data that is mostly numerical simulation and, critically, can also comprise real-world experimental data. In doing so, these models can supersede our first-principles understanding of physics and chemistry and continue to improve at the rate of our ability to generate data and mobilize the requisite compute.
- Full-lifecycle digital twins: The use of numerical simulation is heavily restricted in the engineering lifecycle — being too slow and compute-intensive, and too complex to set up and manipulate — making it impractical for applications like manufacturing, industrial automation, and process control. Because AI models can be more easily adapted for different hardware and are fast to run, they can be used across the whole product development lifecycle, from design to manufacturing to production and operations.
We aren’t setting out to replace numerical simulation nor to do away with physical testing, but to mitigate our customers’ reliance on it ‘in the workflow’, across all the engineering and manufacturing activities and processes that they undertake. Over time, the intent is to shift where and how numerical simulation and physical testing are used because of the bottlenecks they represent ‘in the workflow’, and to move those bottlenecks to data generation, evaluation, and validation for AI models.
Numerical simulation and high-performance computing revolutionized engineering thirty years ago by offsetting a strict reliance on physical testing; we believe we are enabling an even more substantial change to the practice of engineering.
As transformative as the opportunities are, we also believe that the shift to physics simulation by AI inference requires a fundamental redesign of the engineering software stack. Today’s tools make it difficult to manage simulation data across toolchains from different vendors, at any kind of scale, or to reconcile that data with real-world data. These tools aren’t built for developers, nor do they help mobilize scalable compute for training and inference. Our platform:
- Provides a system of record to unify and manage simulation data at scale across the whole engineering lifecycle and a broad vendor landscape;
- Provides scalable infrastructure for organizations to train and fine-tune Deep Physics Models, including private foundation models;
- Provides the components, primitives, and services to build and deploy complex inference-driven engineering workflows for a diverse set of application requirements across the whole enterprise — with as little software engineering complexity as possible.
And critically, our platform provides enterprise-grade security and support for the most security-conscious and regulated industries.
Backed to build for the industries that matter most
Our customers are developing the next generation of semiconductor manufacturing equipment, processing critical minerals, smelting complex alloys and casting high-performance alloy parts, building next-generation aircraft and EVs. We are working with some of the world’s most innovative teams and companies across advanced industries and are committed to bringing dramatic acceleration and the best software to their most important challenges.
Our plan and ambition from inception have been to build a global company relevant to advanced manufacturing across industries. Reflecting that ambition, we have raised $135 million as part of our Series B financing. The fundraising round is led by Atomico, with participation from new investors Temasek, July Fund, Siemens, Applied Materials, and our existing investors, including General Catalyst, NGP, Radius Capital, and Standard Industries. The round brings together a group of investors and companies that share our ambition and are deeply knowledgeable and enmeshed in the industries we are building into. This capital will allow us to accelerate the build-out of our platform, develop larger, more powerful physics foundation models, and expand our global footprint to be more effective force multipliers to the global companies we serve.
We are working to foment a revolution in engineering. It is important and urgent work — in virtue of the importance of what our customers do and all the ways in which our societies depend on what they produce. We are excited about the road ahead and all the building still to come, in both hardware and software. Let’s go faster.